Hidden Costs of Storage Chamber Malfunction
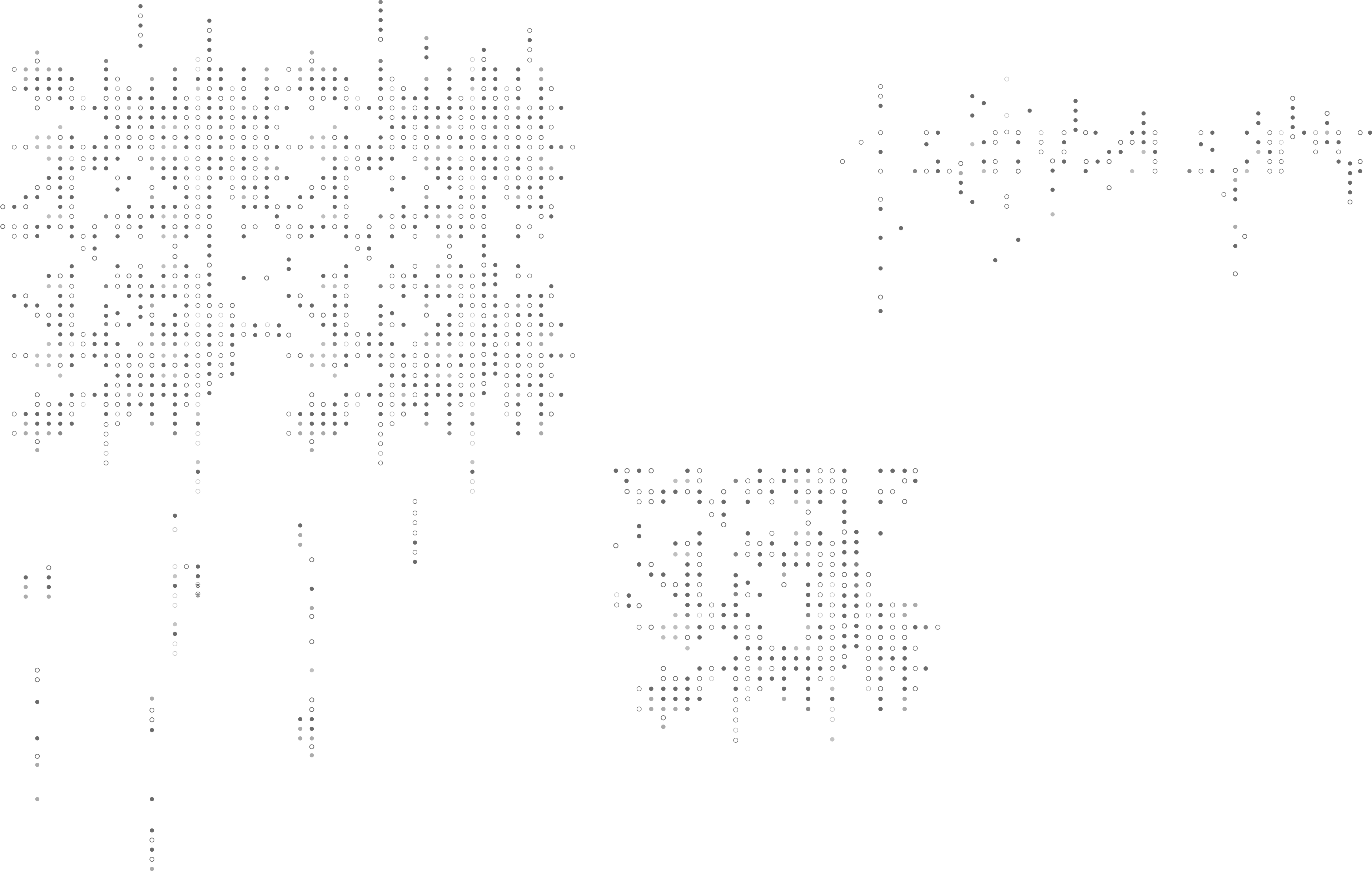
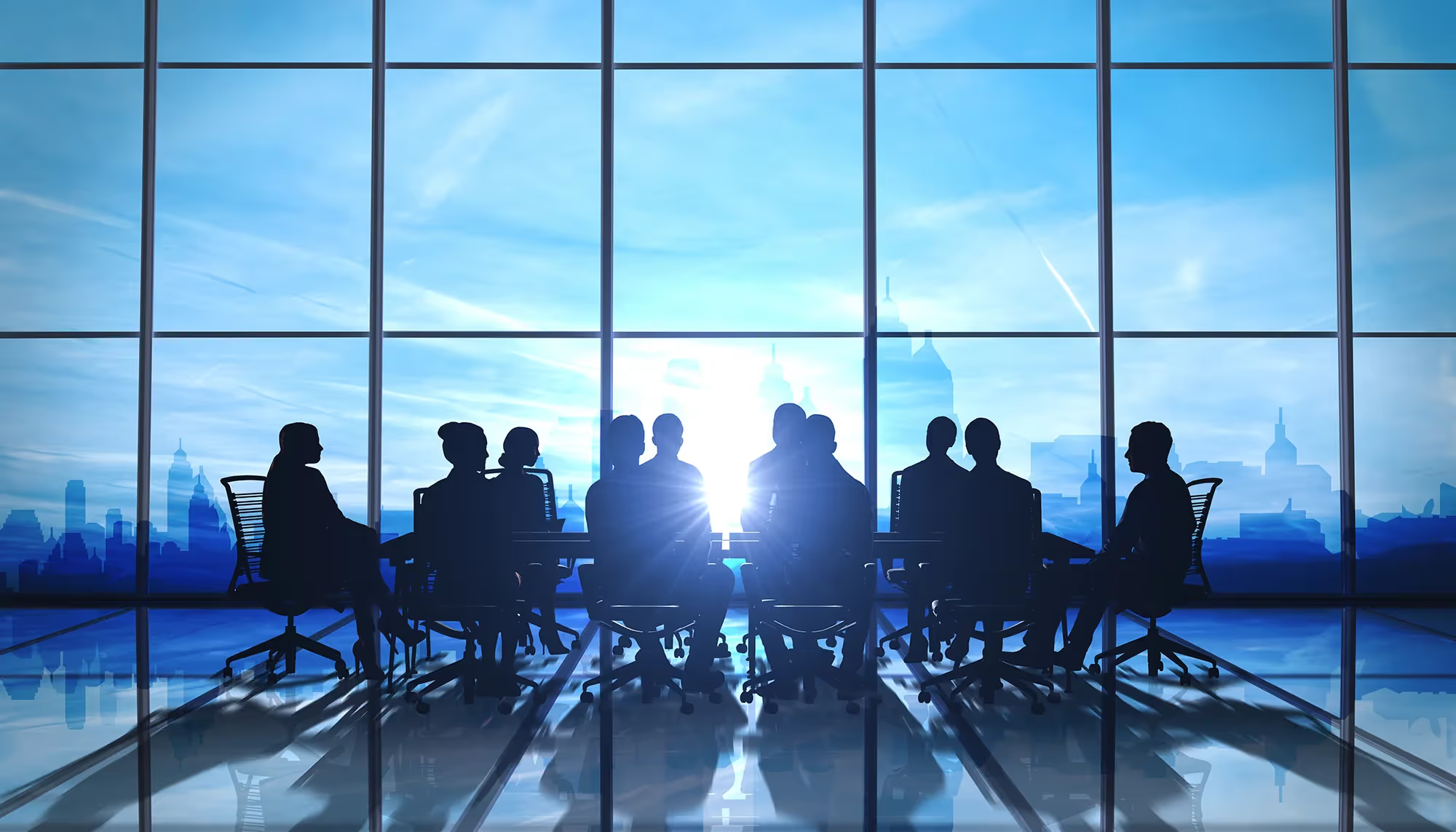
Instroudction
The cost to repair a pharmaceutical storage chamber can widely range depending on the nature of the repair. To swap out a single malfunctioning part could be as low as $200. On the other end of the spectrum, it could cost more than $8,000 if the repair is more extensive and chamber revalidation is needed.
Yet, $8,000 is nothing compared to the true cost of storage chamber malfunction. Aside from the actual repair charge, there are several hidden costs of storage chamber malfunction. Below are four ways that a chamber malfunction can impact a life sciences company.
Legal consequences
When chambers malfunction and the products inside are compromised, there can be legal consequences. For example, in 2018 Pacific Fertility Center in San Francisco, California, experienced a malfunction and one of its nitrogen tanks failed. The failure affected thousands of eggs and embryos from more than 400 families.
In addition to the costs of repairing the nitrogen chamber, the loss of the samples, and the emotional devastation to the patients, Pacific Fertility Center faced significant legal troubles. Five families affected by the freezer tank failure started a lawsuit. The fertility clinic and nitrogen tank manufacturer were held responsible and paid $15 million in damages to the families.
In this case, the legal consequences were monetary. However, it was a landmark case, as it was the first time a jury had awarded damages in a case involving the destruction of eggs and embryos. This sets a precedent for lawmakers to make changes in the regulation of nitrogen tanks and fertility clinics. If a similar equipment failure happens again, the legal action could reach beyond the affected company and manufacturer.
Business disruptions
The loss associated with chamber malfunction goes far beyond the contents or even the chamber itself. The disruption to business can cause rippling financial effects. With a storage chamber out of commission, a pharmaceutical company or contract manufacturing organization may need to halt production because it doesn’t have the capacity to store new products. If the chamber was storing ingredients or unfinished products. The company may not be able to create the products on time, forcing orders to be delayed or even cancelled, which is also a cost to the patients relying on the finished products.
Other business disruptions include the cost of new ingredients for a fresh batch of product, the extra wear-and-tear on the functioning chambers, and the wasted spare parts that went with the malfunctioning unit. These disruptions can cause long-term effects on the bottom line, especially because they are much harder to predict and calculate than routine maintenance costs.
Delayed research and medical progress
When a freezer chamber malfunctions and ruins biological samples, the ramifications can be far-reaching, especially when the samples are irreplaceable. In the worst cases, a malfunction can delay critical research and slow progress in an area of medicine. In essence, the loss of destroyed biological samples can be much greater than the samples themselves, as was the case at the Harvard Brain Tissue Resource Center.
In 2012, a freezer at the Harvard Brain Tissue Resource Center failed. Two alarms should have gone off, but unfortunately, neither did. The freezer was storing brains, many of which were damaged by the thawing. The damaged samples were a massive blow to the facility. About a third of the brains were from people diagnosed with autism. The loss of these research samples has set back autism research by a decade, one neuroscientist said.
Negative PR
If the chamber malfunction is bad enough to hit the news, as in the previous examples, the negative PR can be a substantial hidden cost. Trust in a company is invaluable; if a company doesn’t handle the situation carefully, it could spend a long time trying to rebuild its reputation.
Even if the malfunction doesn’t make the news, the word can still spread and scare off customers—current and potential. Once customers experience a delay or backorder because of the freezer chamber malfunction, they might not return for business.
Lowered employee morale
A failed freezer chamber can negatively affect employee morale. Maintenance staff may especially feel the stress of such an incident. If employees can’t trust the equipment, they may not feel they can adequately perform their duties. Once the chamber is fixed or replaced, employees may feel pressure to work extra hard to make up for lost time and product.
How to protect yourself from major malfunctions
The best way to avoid these hidden costs is to keep walk-in chambers in optimal condition. While routine preventive maintenance can be helpful, predictive maintenance is a much smarter way to avoid catastrophes. Predictive Monitor gathers data to help stop major malfunctions before they even happen.