Preventive Monitoring vs. Predictive Monitoring
Preventive Monitoring vs. Predictive Monitoring
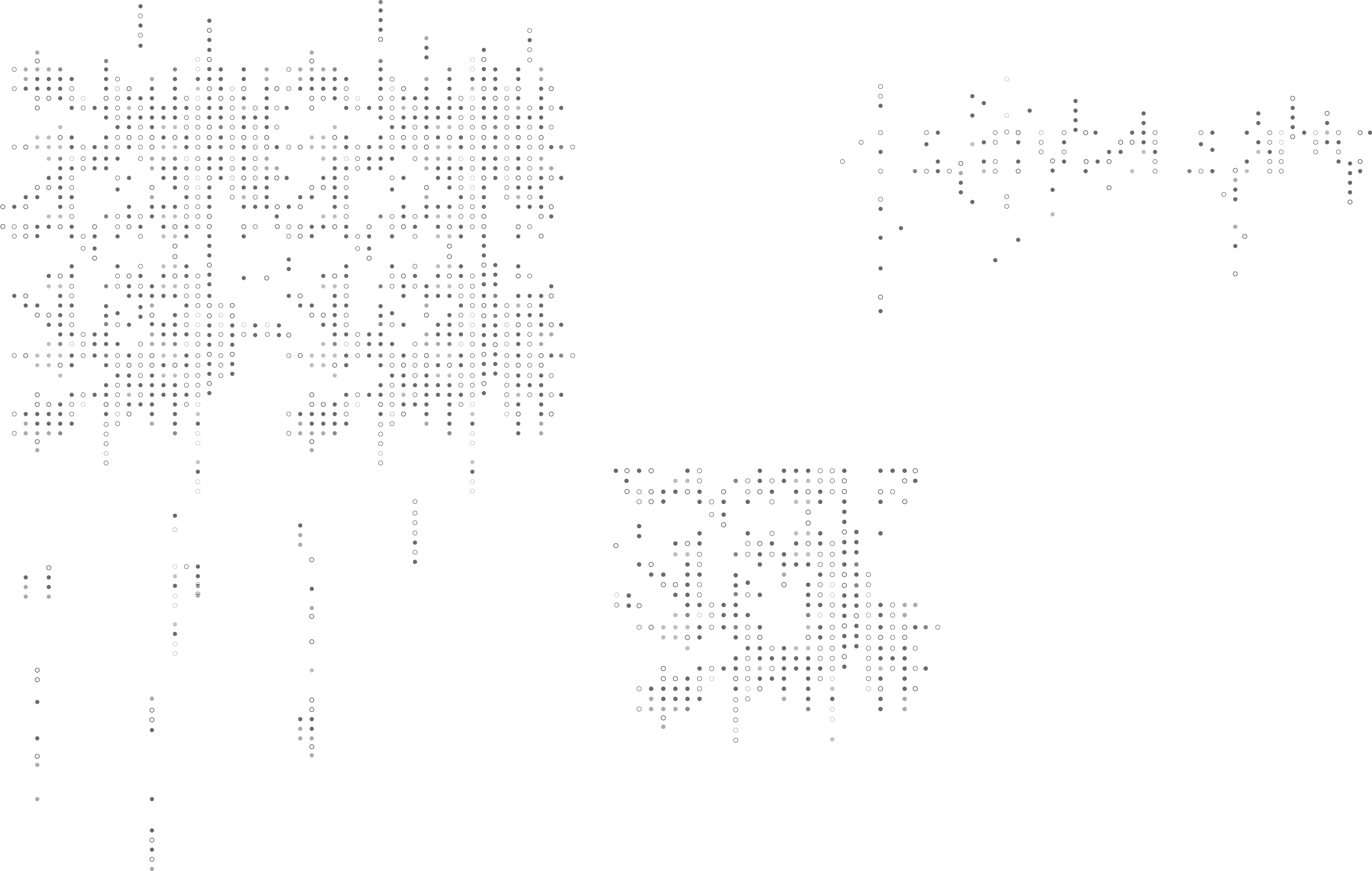
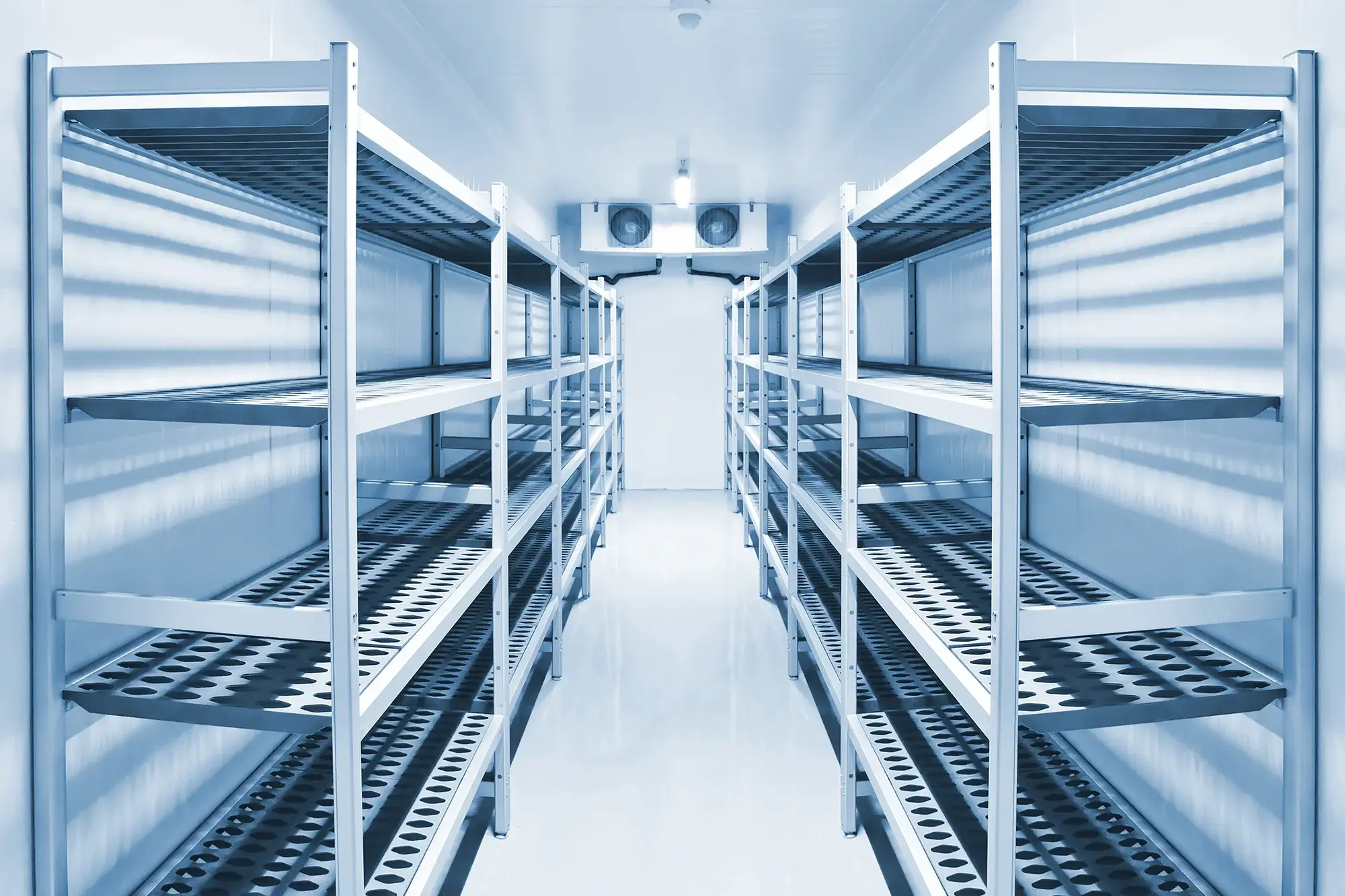
No company wants to deal with equipment downtime, but this is especially true for life sciences companies manufacturing and storing drug products. A malfunction in a walk-in refrigeration unit is not the same mild inconvenience as a malfunction in a computer printer. The safety and efficacy of life-saving medicine are dependent on the storage chamber operating in optimal condition.
That’s why for decades, life sciences companies have relied solely on environmental monitoring systems to ensure medicines and other priceless products stay safe and effective. While the technology behind these systems has evolved, the approach has remained the same—prevent product spoilage by identifying potentially dangerous shifts in storage chamber temperature.
Preventive monitoring has largely remained the sole industry standard until now. Innovative, forward-thinking companies are transforming the industry by implementing predictive monitoring.
Read on to understand the difference between preventive and predictive monitoring. Then find out how predictive monitoring can help shift businesses from reactive to condition-based maintenance.
What is preventive monitoring?
Traditional, preventive monitoring systems monitor with the purpose of checking for temperature irregularities. When there is an irregularity, maintenance teams are typically alerted by a call, SMS, and email. Regardless of the time of day, the team reacts quickly to fix the issue and ensure the product is safe.
With traditional monitoring systems, there is planned downtime—preventive maintenance. On a regular schedule, employees check specific equipment and supplies for common malfunctions, preset expiration dates, and certain capabilities. This system is convenient for busy companies because they can plan around it. The trouble with this type of prevention is that it doesn’t always catch the things that can go wrong between routine inspections. Therefore, complete protection from catastrophe isn’t guaranteed. There’s also the accompanying stress of dropping everything to save the products and fix the failed equipment.
What is predictive monitoring?
Predictive monitoring is a new, proactive way of understanding equipment and supplies. Fueled by tiny, strategically placed sensors, predictive monitoring identifies irregularities in refrigeration systems, catching problems before they happen. Predictive monitoring uses data to identify when parts need replacing before critical refrigeration systems fail and destroy priceless pharmaceutical products.
Benefits of predictive monitoring
As life sciences companies move from relying solely on scheduled, reactive, preventive maintenance to incorporating condition-based, predictive maintenance, they’ll gain several advantages.
- More efficient maintenance processes. Predictive monitoring helps streamline the maintenance process. Companies will repair only the pieces that are performing poorly or are most at risk of damage rather than checking each unit on the same schedule. They can also be more efficient in ordering replacement parts and extending the life of their equipment. If backup equipment isn’t used often, it may not need maintenance as frequently.
- Less unexpected downtime. With predictive monitoring, companies can avoid downtime from unexpected mechanical failures. If the data identifies an irregularity, it’s much cheaper and faster to fix a malfunctioning part than pay thousands of dollars to replace the entire piece of equipment after a major failure. Companies can incorporate maintenance into production timelines allowing them to continue manufacturing products instead of struggling with delays for major repairs.
- Improved company culture. Predictive monitoring is also beneficial to company culture and morale. Maintenance workers can worry much less about dealing with stressful emergencies. With more streamlined maintenance, companies can maximize the efficiency of their workforce, which is critical given the current challenges in the life sciences labor workforce.
Implementing a predictive monitoring system
In a predictive monitoring system, data is recorded from strategically placed sensors in the equipment. After enough data has been collected and a baseline is established, the system can begin to analyze the equipment trends. The system will identify potential equipment problems or anomalies based on the trends. The more data the system has, the more accurate the predictions.
On the company’s end, there is very little they need to do except heed the warnings and take action when action is suggested. Early detection allows companies to resolve issues without the stress and panic of chamber failure.
Saving money and lives
Predictive monitoring can save pharmaceutical companies money by improving maintenance procedures, avoiding equipment downtime, and enhancing company culture. However, predictive monitoring can also help save lives.
Patients depend on vaccines, personalized medicine, patient samples, and other biological materials typically stored in a walk-in refrigeration unit. Business may be in jeopardy if a disaster occurs within one of these units, but patients have the most to lose because their lives depend on those products.
When pharmaceutical and life sciences companies use predictive monitoring to avoid equipment downtime, their products are more consistently available. When life-saving products are consistently available, it’s a win-win for the patients and the companies whose mission is to save lives.
See OverShield in Action
Outcomes
Conclusion
Product Gallery
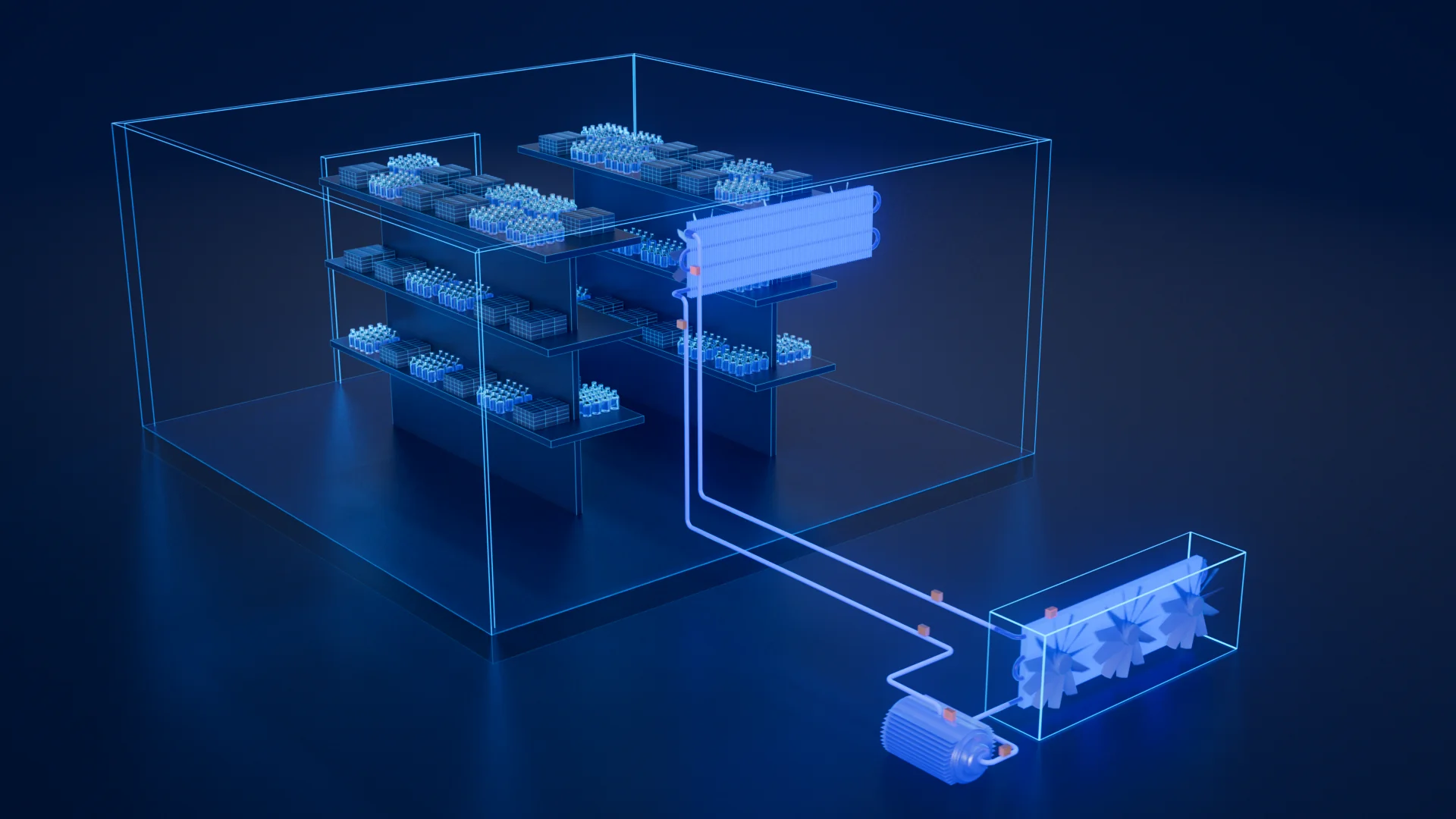
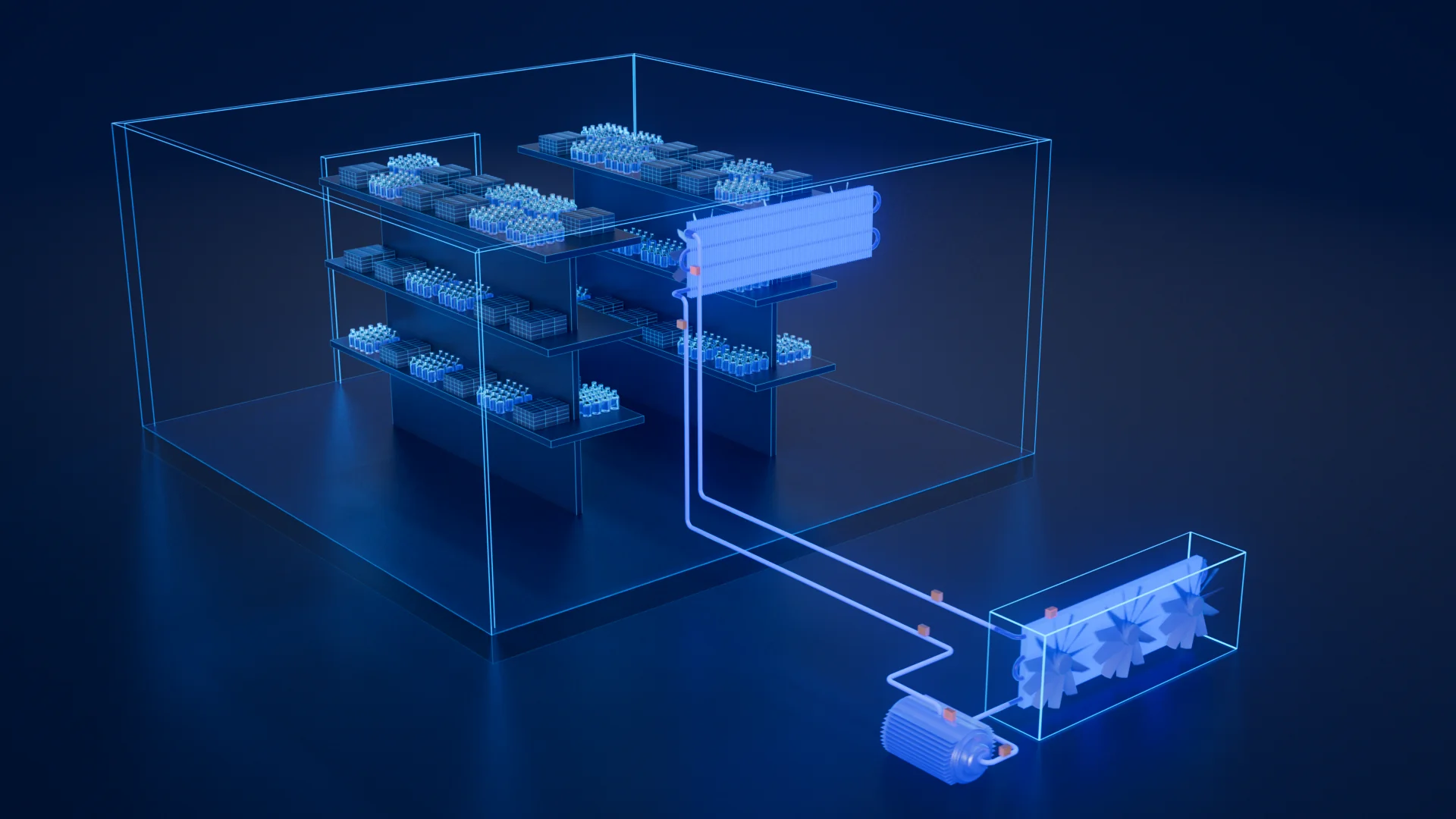
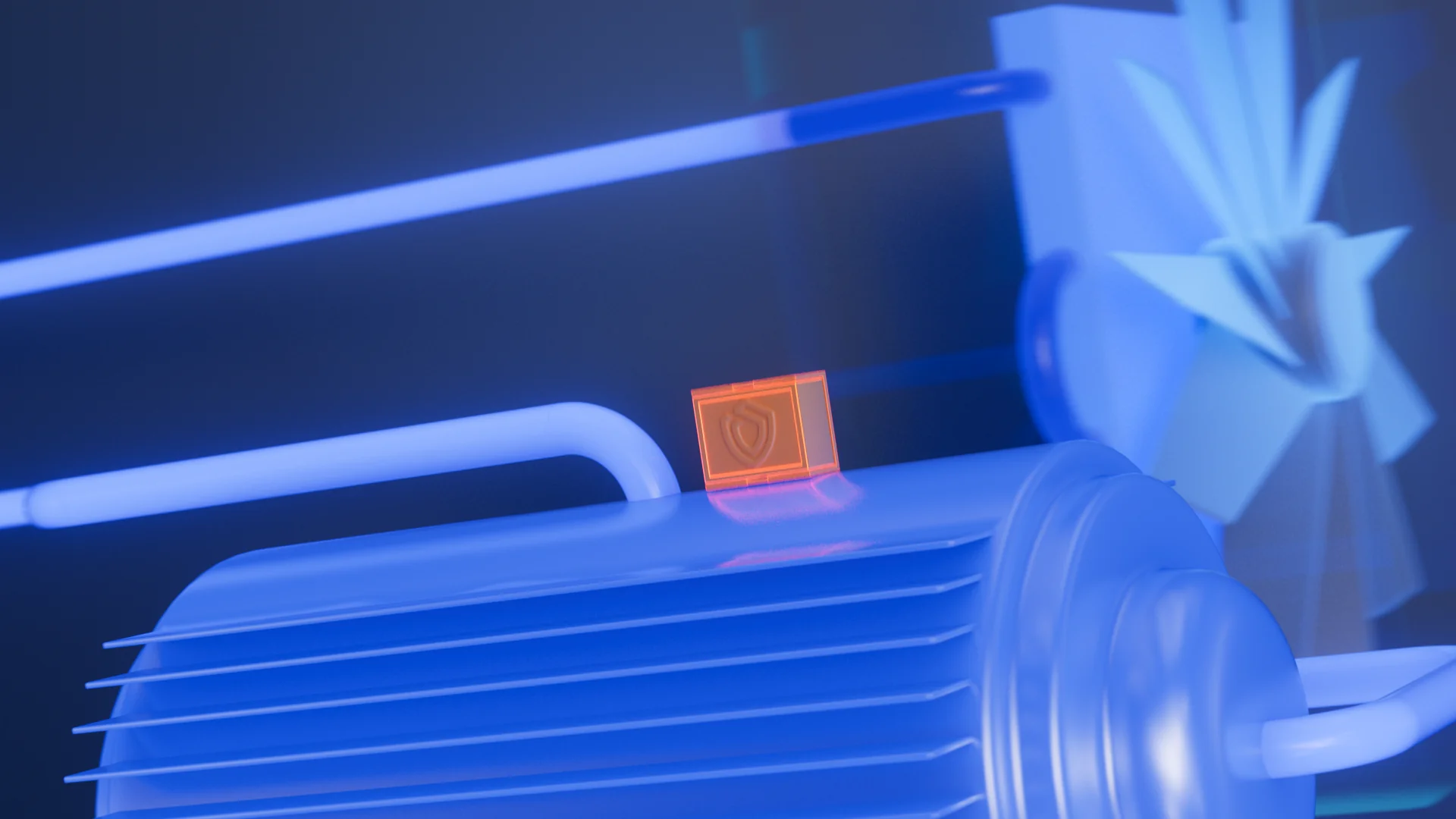
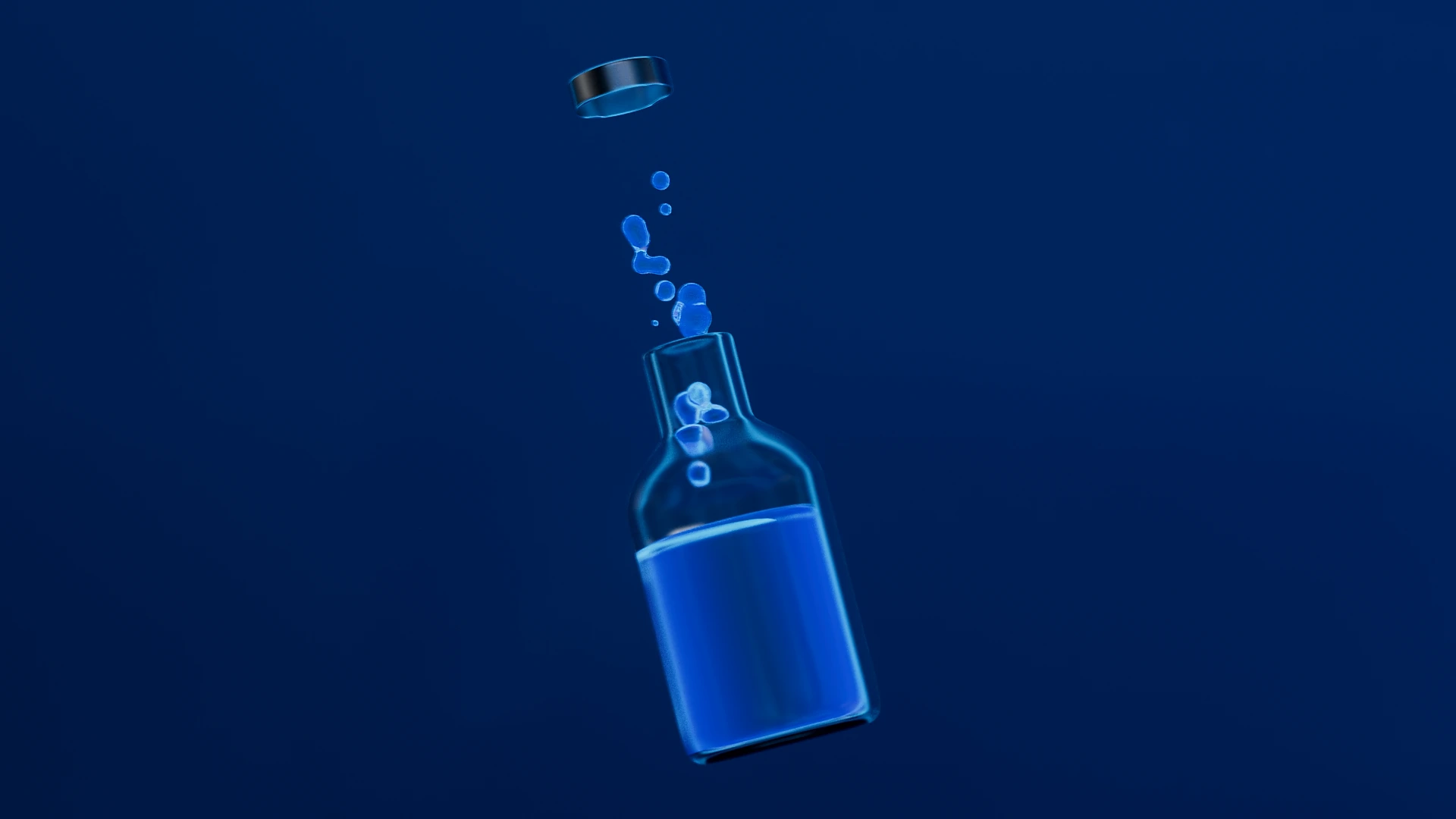
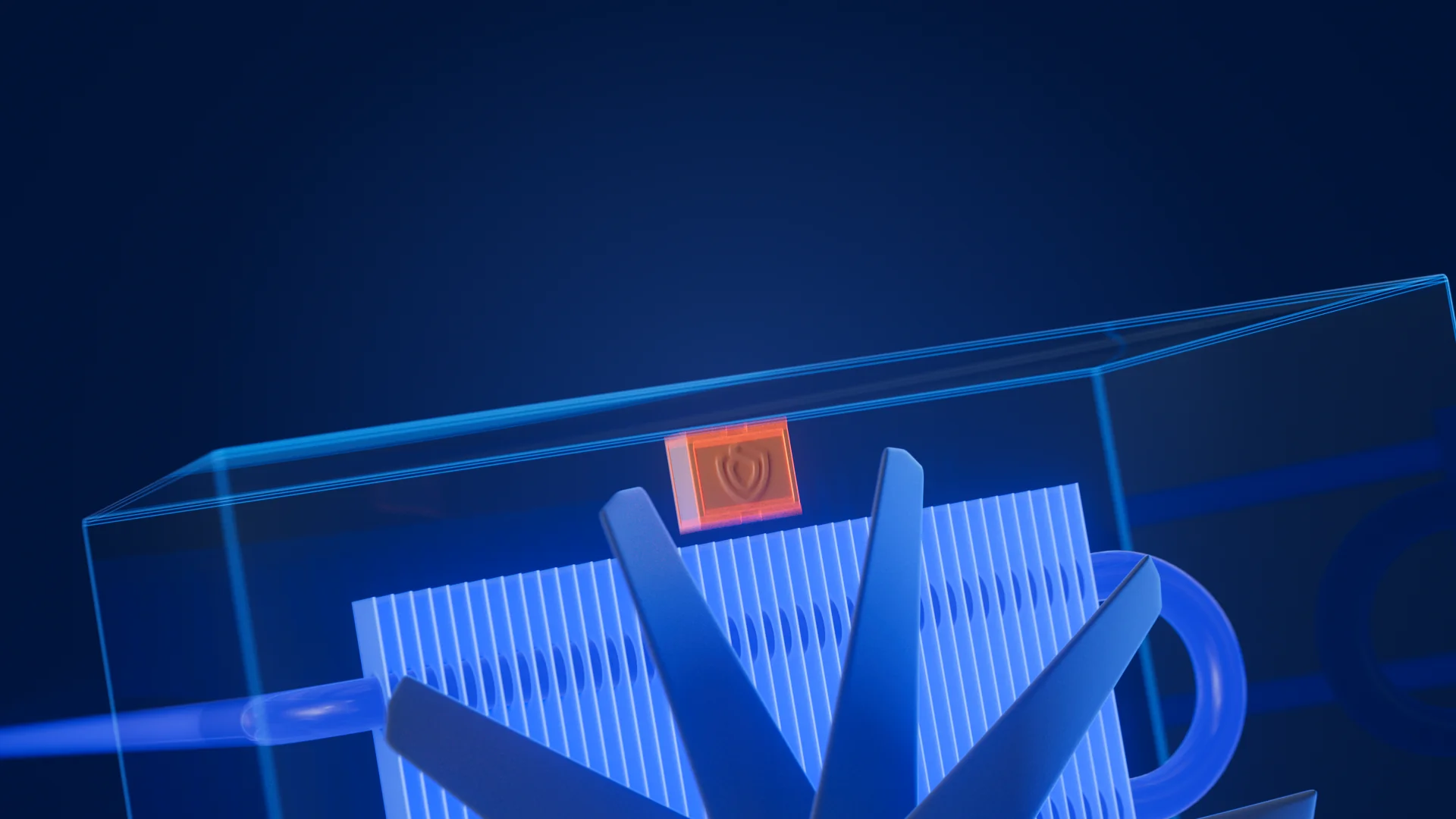